CORROSION TEST FOR ELECTRIC VEHICLE COOLANTS IN GLASSWARE ASTM D 8485
CORROSION TEST FOR ELECTRIC VEHICLE COOLANTS IN GLASSWARE ASTM D 8485
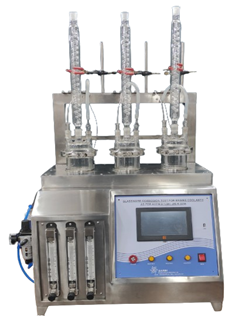
The Vapour phase and submerged copper corrosion by wire resistivity
method for EV lubricating & cooling fluids
Model: SEWEVCC01
This equipment is capable of studying the impact of hydrocarbon & aqueous fluids on electrical conductivity of the copper substrates. It studies the impact of vapours on the electrical conductivity of the copper wires/coupons when the copper wires/coupons come in contact with the vapours of the hydrocarbon/ aqueous fluids. Also, it determines the change in electrical conductivity due to corrosion of the electric wires/coupons when dipped in samples during the test. The equipment is capable of running two test samples simultaneously. Entire Range of Performance testing Equipment For Lubricants, Greases, Fuels, coolants, Brake fluids. Etc. and Metals, Alloys & Elastomers Test Coupons.
The corrosion rate in presence additive components can be studied upon by this method and provides details which are generally are not obtained from traditional corrosion tests and insight as to how to formulate oils / coolant system to better protect copper and copper alloys. The corrosion study for the base fluid with and without additive package or fluids with different additive package systems can be studied. The relative change in resistivity can be quantified as user’s requirement. The graph resistance vs time helps in interpreting copper corrosion pattern. The time-lag factor for any appreciable change in resistance indicates the additives consumption over the time. One can study effectives of corrosion inhibitor or the package.
Aluminum heating blocks | The heating is provided by solid aluminum block which are housed in stainless steel bath. Each beaker has dedicated aluminum bath, the temperature of which can be set up independently. |
Rotameter(Flow Control) | It indicates the flow rate of air into the beaker. The flow rate can be adjusted with the help of a flow control valve provided. (Recommended flow rate by standard is 100 cc/min). |
Temperature Sensors | The temperature sensors are of RTD type immersed in the testing fluid. They supply the temperature information to the temperature controller, which in turn controls the temperature of the heating bath. |
Beaker | A 1000-ml, tall -form, designed as per standard, spout less beaker, made of heat resistant glass, for containing the engine coolant solution and test specimens. The beaker shall be tightly closed with the provided thick cover, having holes to accommodate a Water condenser, Aerator tube and Temperature Sensor. |
Condenser | A reflux tube type water condenser manufactured of heat resistant glass having 400-mm long condenser jacket is used as per the standard. Condenser Clamps with stand used to hold and support the condenser in position within the test beaker are provided. |
Aerator Tube | The Gas dispersion tube with standard pores are used to disperse air through the sample as per the standard. |
Beaker Stand | The beaker stand is placed in the heating bath to support and hold the beaker which is placed on the beaker stand during the test operation. |
Auxiliary Stands | The auxiliary stands are provided to support condenser clamps and to support/ hold Aerator tubes, temperature sensors etc. when not in use. |
Control Panel | The HMI, touch screen control panel & other components are housed in SS enclosure. Other control panel components consists of all the instruments such as temperature controller cum digital indicators with continuous display, contactors, switches, relays, MCBs, etc. required for all test assemblies. Salient features of control panel. |
Extra free spares and consumables included in scope of supply |
|
Not included in scope of supply |
|
Installation requirement |
|