COPPER CORROSION TESTER FOR EV FLUIDS
COPPER CORROSION TESTER FOR EV FLUIDS
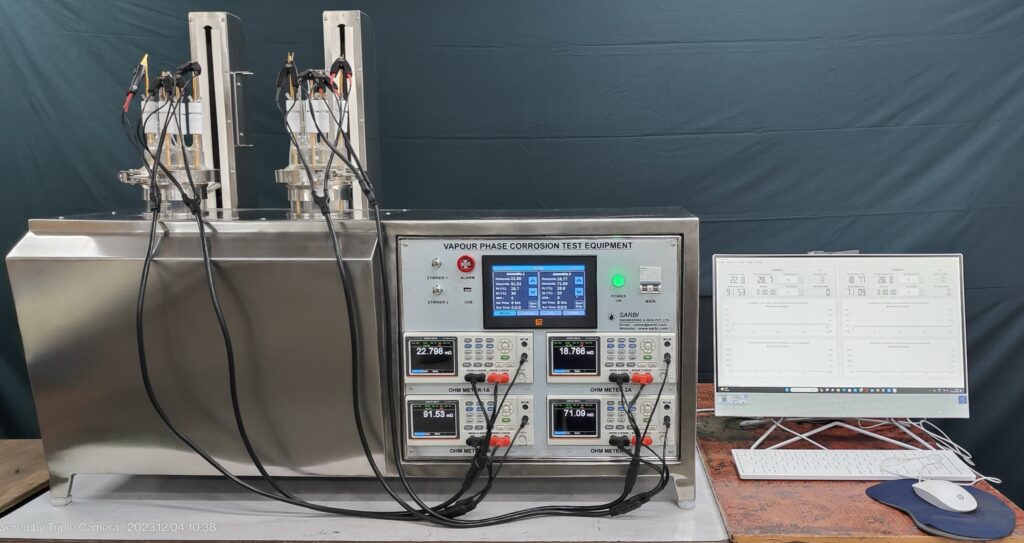
This test method covers a simple beaker-type procedure for evaluating the effects of glycol-based electric vehicle coolants on
metal specimens under controlled laboratory conditions.
This test method evaluates the corrosion on test specimens of
stainless steel and aluminum, with an option for a copper test
specimen ,And evaluates coolants without the addition of any
corrosive elements.
In this method, specimens of metal typical of those present in electric
vehicle cooling systems are totally immersed in aerated coolant
solutions for 336 h at 88 °C. The corrosion inhibitive properties of the test solution are evaluated on the change in weight incurred by the
specimens. Each test is run in triplicate, and the average weight
change is determined for each metal.
COPPER CORROSION TESTER FOR EV FLUIDS
SUMMARY OF TEST METHOD
In this test method the electric wire dipped (submerged) in oil to determine the change in electrical conductivity due to corrosion and the copper coupon hanging ( Vapour phase corrosion) in a beaker to study the impact of vapors on the electrical conductivity of copper coupon for the specific time and temperature of the oil. The test design is shown in Figure 1 and 2 and consists of a 1-m-long, 0.5 mm diameter
copper wire of 99.9% purity submerged in the test fluid with a direct current of 1 mA applied.
To determine vapour phase corrosion, a representative printed circuit board panel of the size 60 x 6 x 2 mm is used in hanging position.
The wire & panel resistance measured in the test is governed by Ohm’s law.
SUGGESTED EXPERIMENTAL CONDITIONS
1) Duration of the test: 50 to 250 h
2) Block Temperature Range: Up to 250°C.
3) Sample Temperature: Up to 160°C
A constant current of 1 milliamp DC is applied by means of a resistance temperature detector (RTD) data acquisition module whose specific task is to measure temperate from RTD devices, the standard being a PT100 which exhibits a resistance of 100Ω at 0°C. Data is acquired by means of a compact data acquisition chassis controller that houses the data acquisition module. This is networked to a local host computer for processing and logging. There is high-frequency data acquisition (10 kHz) and a variable deterministic resistance logging rate, which in this case is every 10 s. The electrical resistance of copper wires is used only to monitor the corrosion that occurs and no resistive or ohmic heating induced corrosion is generated.